“Ensuring Industrial Safety and Performance with Actuator Valve Testing Methods”
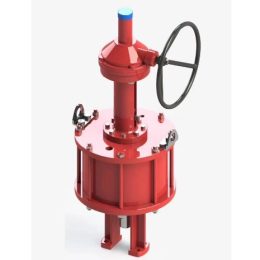
Actuator Valve Testing
Actuator valve testing is an essential part of ensuring the performance and safety of industrial processes. Properly functioning actuator valves are crucial for the efficient and reliable operation of systems such as pipelines, power plants, and chemical processing plants. There are several methods for testing actuator valves, including hydraulic, pneumatic, electrical, and diaphragm testing, each with its own advantages and limitations.
Hydraulic Actuator Valve Testing
Hydraulic actuator valve testing involves the use of hydraulic fluids to move the valve stem and test its performance. This method is particularly useful for testing high-pressure valves that require a lot of force to operate. To perform hydraulic actuator valve testing, a hydraulic pump is used to apply pressure to the valve, and the resulting movement of the valve stem is measured and recorded. The test can also include monitoring the pressure drop across the valve and the valve’s ability to maintain a stable position under varying pressures.
Pneumatic Actuator Valve Testing
Pneumatic actuator valve testing is similar to hydraulic testing but uses compressed air or gas instead of hydraulic fluid. This method is commonly used for low-pressure valves and is easier to control than hydraulic testing. During pneumatic testing, the valve is pressurized with compressed air, and the resulting movement of the valve stem is measured and recorded. Like hydraulic testing, pneumatic testing can also include monitoring the pressure drop across the valve and the valve’s ability to maintain a stable position under varying pressures.
Electrical Actuator Valve Testing
Electrical actuator valve testing involves the use of an electric motor to move the valve stem and test its performance. This method is particularly useful for testing valves that require precise positioning, such as control valves. During electrical testing, a motor is connected to the valve stem, and the motor’s movement is measured and recorded. The test can also include monitoring the valve’s ability to respond to different control signals and its ability to maintain a stable position under varying loads.
Testing for Diaphragm Actuator Valve
Diaphragm actuator valve testing is a specialized method used for testing valves that use a diaphragm to move the valve stem. This method involves pressurizing the diaphragm and measuring its movement and response. Diaphragm testing can also include monitoring the valve’s ability to maintain a stable position under varying pressures and loads.
Importance of Actuator Valve Testing===
Actuator valve testing is essential for ensuring the safety, efficiency, and reliability of industrial processes. Using the proper testing method can help identify potential valve failures before they occur, preventing costly downtime and equipment damage. By regularly testing actuator valves, maintenance teams can ensure that valves are operating at optimal levels and reduce the risk of unexpected failures.
- Each Part of the Valve
- Understanding Globe Valves: Advantages, Disadvantages, and Uses
- Introduction of Anti-Corrosion Methods for Valve Parts
- Why Should the Shut-Off Valve Have Low Inlet and High Outlet?
- How Swing Check Valves are Tested and Inspected: A Comprehensive Guide
- Efficient and Versatile: The Casted Floating Ball Valve for Industrial Applications