Unlocking the Performance of Pneumatic Actuated Butterfly Valves
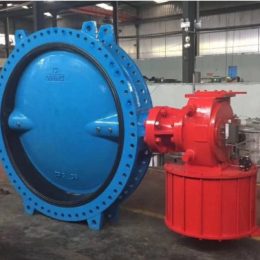
Unlocking the Performance of Pneumatic Actuated Butterfly Valves
Pneumatic actuated butterfly valves are widely used in many process industries because of their reliability, simplicity, and cost effectiveness. These valves are designed to control the flow of fluid in pipelines, and their performance depends on the accuracy and efficiency of the pneumatic actuation system. Proper actuation of these valves is crucial for achieving optimal control and maximizing valve functionality. In this article, we will explore the various techniques and strategies to unlock the full potential of pneumatic actuated butterfly valves.
Unleashing the Full Potential of Pneumatic Actuated Butterfly Valves
Pneumatic actuated butterfly valves offer many advantages over other types of control valves, such as gate valves and ball valves. They are lightweight, compact, and require minimal maintenance. However, to unleash their full potential, it is important to optimize the actuation system for maximum efficiency and accuracy. This can be achieved by selecting the right actuator size, selecting the right actuation speed, and ensuring the proper alignment of the actuator with the valve stem.
Boosting Fluid Control Efficiency with Pneumatic Actuation
Pneumatic actuated butterfly valves are widely used in many process industries because of their ability to control the flow of fluid accurately and efficiently. The pneumatic actuation system plays a crucial role in achieving this efficiency. By selecting the right actuator and optimizing the pressure and flow rate of the compressed air, fluid control efficiency can be boosted significantly. This results in better process control, reduced energy consumption, and less wear and tear on the valve components.
Overcoming Challenges in Pneumatic Actuator Optimization
Optimizing the pneumatic actuation system of butterfly valves can be challenging, especially in harsh process environments that expose the valves to high temperatures, pressures, and corrosive fluids. To overcome these challenges, it is important to select the right materials for the valve components, ensure proper maintenance of the actuation system, and implement safety measures to prevent valve failure. This requires a thorough understanding of the process conditions and the limitations of the valve components.
Maximizing Valve Functionality through Proper Actuation
Pneumatic actuated butterfly valves are designed to perform specific functions in process industries, such as isolation, regulation, and diversion of fluid flows. To maximize their functionality, it is important to select the right valve size, ensure proper installation and alignment, and optimize the actuation system for the specific process conditions. This ensures optimal performance and reduces the risk of valve failure or malfunction.
Enhancing Valve Performance with Pneumatic Actuation Techniques
Pneumatic actuation techniques, such as positioners, limit switches, and feedback sensors, can enhance the performance of butterfly valves by providing accurate and real-time information about the valve position, flow rate, and pressure. This information can be used to adjust the actuation system and optimize the valve performance for maximum efficiency and accuracy. These techniques also enable remote control and monitoring of the valve operation, which is crucial for process automation and safety.
Achieving Optimal Control with Advanced Pneumatic Actuator Designs
Advanced pneumatic actuator designs, such as smart actuators and proportional control systems, offer even greater control and accuracy in the operation of butterfly valves. These designs use advanced sensors, controllers, and algorithms to optimize the valve performance for specific process conditions, and provide real-time feedback and control. This results in precise and efficient fluid control, reduced energy consumption, and increased process safety.
Unlocking the full potential of pneumatic actuated butterfly valves requires a thorough understanding of the actuation system, the valve components, and the process conditions. By selecting the right actuator size, optimizing the pressure and flow rate of the compressed air, and implementing advanced actuation techniques, optimal control and efficiency can be achieved. Proper maintenance and safety measures are also crucial to ensure valve functionality and prevent valve failure. With the right strategies and techniques, process industries can maximize the performance and reliability of their pneumatic actuated butterfly valves.