“Understanding Safety Valves: Types, Selection, Installation, and Maintenance”
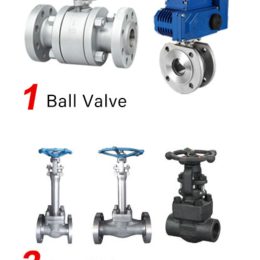
Understanding Safety Valves
Safety valves are an essential component of most industrial systems, designed to prevent overpressure and minimize damage caused by explosions or bursting. Proper usage of safety valves can help prevent accidents and ensure the safety of personnel and equipment. In this article, we will discuss the different types of safety valves, guidelines for proper selection and installation, testing and maintenance procedures, and common problems and troubleshooting techniques.
Types of Safety Valves and Their Applications
There are different types of safety valves, including spring-loaded, pilot-operated, and balanced bellows safety valves. Spring-loaded safety valves are commonly used in industrial processes, while pilot-operated safety valves are used in high-pressure applications. Balanced bellows safety valves are used in applications that require high sensitivity and accuracy. Safety valves can also be classified based on the type of fluid they handle, such as steam, gas, or liquid.
Guidelines for Proper Selection and Installation
Proper selection and installation of safety valves are crucial to their effectiveness. Safety valves should be selected based on factors such as the type of fluid, operating pressure, and temperature. The size of the safety valve and the discharge piping should be properly matched to prevent backpressure. Safety valves should be installed in a vertical position, with the discharge pipe directed to a safe location. The installation should also include isolation valves and pressure gauges for monitoring.
Testing and Maintenance Procedures for Safety Valves
Safety valves should be regularly tested and maintained to ensure their proper functioning. Testing should be done periodically to determine whether the valve opens at the designated set pressure and closes properly after release. Maintenance should include cleaning, lubrication, and replacement of worn-out parts. The frequency of testing and maintenance should be determined by the operating conditions and industry standards.
Common Problems and Troubleshooting Techniques
Common problems with safety valves include leakage, chatter, and corrosion. Leakage can be caused by worn-out seals or corrosion. Chatter can be caused by the valve opening and closing rapidly, creating vibration and noise. Corrosion can occur due to exposure to the fluid, leading to reduced efficiency or complete failure of the valve. Troubleshooting techniques include visual inspection, testing, and replacing worn-out parts.
Importance of Safety Valve Usage
In summary, safety valves play a critical role in ensuring the safety of personnel and equipment in industrial processes. Proper selection, installation, testing, and maintenance of safety valves are essential to their effectiveness. The use of safety valves can prevent accidents, minimize damage, and increase productivity. By following the guidelines and tips discussed in this article, industries can ensure the safe and efficient operation of their systems.