3 Types of Control Valves: Linear Motion, Ball, and Globe
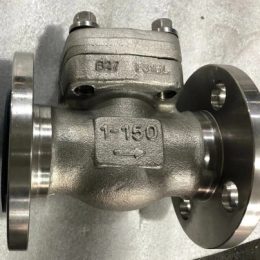
Control valves are one of the essential components in the process control industry. They regulate the fluid flow and pressure in pipelines, and they play a critical role in maintaining system performance. There are many types of control valves, but this article will focus on three primary types: linear motion, ball, and globe valves. We will explore the differences between these valves, their applications, and how they work.
Understanding Linear Motion Valves
Linear motion valves, also called sliding stem valves, use a linear motion to control the flow of fluids through a pipeline. This type of valve has a stem that moves up and down, and the linear movement of the stem regulates the flow of the fluid. Linear motion valves are commonly used in applications that require precise control, such as in chemical processes or pharmaceutical manufacturing.
Linear motion valves come in two types: globe and angle valves. Globe valves are used for throttling or regulating flow, while angle valves are used for on-off service. The advantages of linear motion valves include their accuracy, repeatability, and good sealing capabilities. However, these valves have a limited range of motion and can be slow to operate.
Exploring Ball Valves
Ball valves use a spherical ball with a hole in the center to control the flow of fluids. The ball is rotated 90 degrees by a handle or actuator to either shut off the flow or allow it to pass through the open center. Ball valves are commonly used in applications that require quick, on-off control, such as in HVAC systems or water treatment plants.
Ball valves have several advantages, including their ability to handle high flow rates, their low friction loss, and their simple design. However, ball valves are not suitable for precise control or throttling applications, and they may not seal well at low or high temperatures.
Examining Globe Valves
Globe valves have a disc that moves perpendicular to the flow of fluid to control the flow rate. The disc is connected to a stem that moves up and down, and the flow rate is regulated by adjusting the position of the disc. Globe valves are commonly used in applications that require precise control over the flow rate or pressure, such as in steam systems, chemical plants, or refineries.
Globe valves have several advantages, including their good sealing capabilities, their ability to handle high pressure drops, and their low noise level. However, globe valves can be slow to operate and may have a higher pressure drop than other types of valves.
Comparing the Three Types of Valves
The choice of valve type depends on the specific requirements of the application. Linear motion valves are suitable for precise control, ball valves are suitable for quick on-off control, and globe valves are suitable for precise control over the flow rate or pressure. Each type of valve has its advantages and disadvantages, and it is essential to consider factors such as fluid type, temperature, pressure, and flow rate when selecting a valve.
Conclusion and Future Directions
In conclusion, control valves are critical components in the process control industry, and the choice of valve type depends on the specific requirements of the application. Linear motion, ball, and globe valves are three primary types of control valves, each with its advantages and disadvantages. In the future, advances in materials, manufacturing, and automation technologies will lead to the development of more efficient, accurate, and reliable control valves.